PepsiCo Coventry has been working with MGTS for over 15 years in a really collaborative partnership. Our candidates return from MGTS to go on to really successful careers within PepsiCo. We have had Junior and Mature apprentices following robust programmes, building fantastic logbooks and knowledge on 4 year tailored courses that perfectly prepare them for engineering technical roles. I would recommend any business looking to switch or start their apprenticeship journey with MGTS.
Why MGTS?
MGTS is an engineering skills training company that has been providing top quality, industrially relevant courses to organisations from around the UK for over 50 years.
We deliver a comprehensive range of Open Courses from our Technical Centres in Coventry and Redditch and specialise in listening to customers’ current and future needs to design training programmes to transform the skills and technical competences of workforces.
- Our Technical instructors are all qualified engineers from within industry and have extensive teaching experience, so you will be learning from the best.
- A comprehensive range of courses on offer at competitive prices.
- Selected courses can be delivered conveniently at your own site.
Available Courses
Please find below a selection of our Training Courses.
Simply click on the course title to view and download a course outline.
To make a booking or discuss bespoke training packages please contact
Viv Kendrick on 024 7663 0333 / enquiries@mgts.co.uk to discuss your training needs.
Kindly ensure any dietary requirements are stated at the time of booking.
View our Course Booking Terms & Conditions / Download a New Customer Application Form
- Electrical Maintenance Module 1
Safe working and isolation of industrial electrical equipment - Electrical Maintenance Module 2
Fault finding of motor control circuits and equipment - Electrical Maintenance Module 3
Interrogation of PLC and inverter drives to aid fault finding and adjustment - Automation & Controls
Motion and Process Control within Automation - Introduction to Siemens PLC
- Introduction to Robotics
- Electrical Panel Access
- 18th Edition BS7671:2022
- PAT Testing C&G2377-77
- Site Electrical Duty Holder
- Technical Fault Finding
- Mechanical Maintenance
- Introduction to Pneumatics
- Introduction to Pneumatics
& Electro Pneumatics - Introduction to Hydraulics
- Abrasive Wheels
- Manual Handling
- MAG Welding
- Manual Metal Arc Welding
- TIG Welding
- Mentoring Apprentices
- Mentoring FDME Apprentices
- HNC in General Engineering
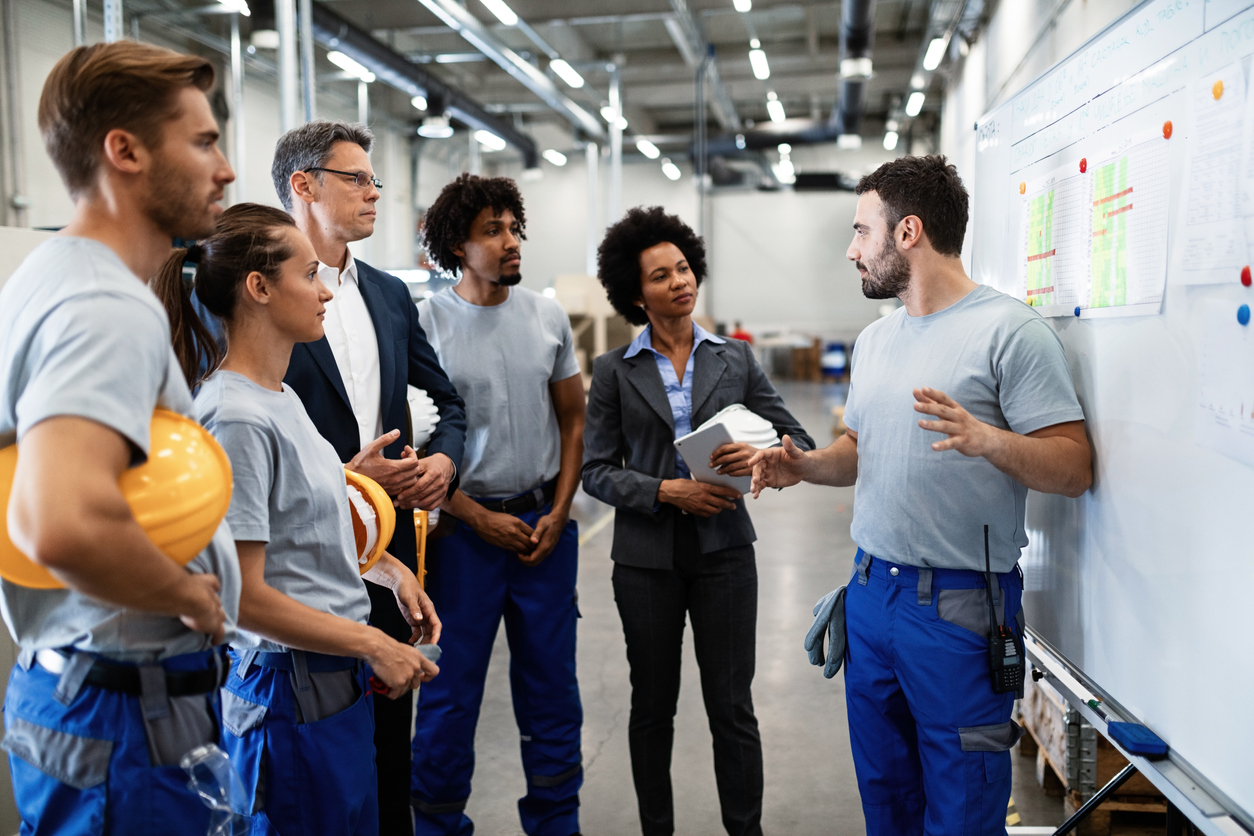
Tailored Courses
Many of our customers request tailored programmes to meet specific business and individual development and assessment needs.
We are delighted to work with our customers to design and support such programmes to develop the technical competences of their employees. Talk to us today to see how MGTS can create bespoke training packages to meet your unique needs.
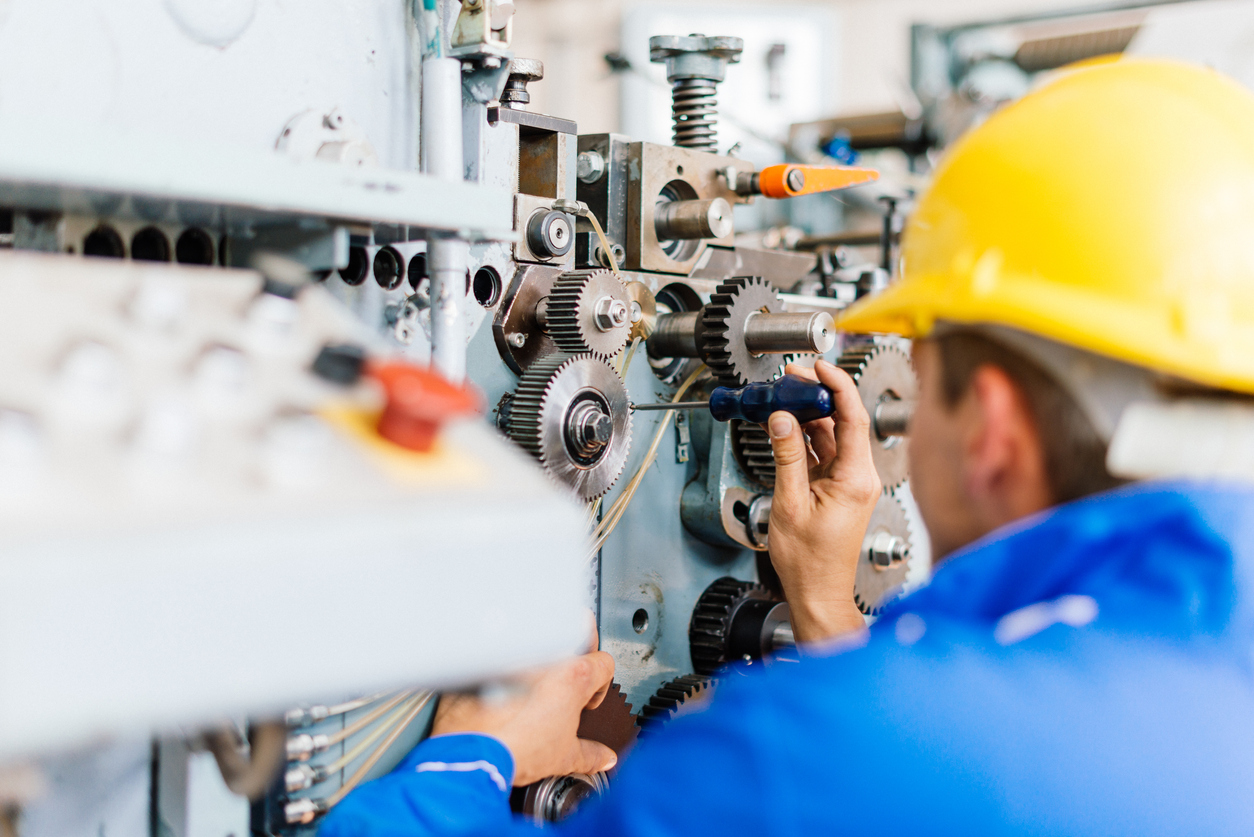
Skills Analysis
MGTS have developed programmes to provide a comprehensive assessment of engineering maintenance and manufacturing technicians’ competences. Where the candidate’s current technical skills, knowledge, attitude and aptitude are required to be assessed for recruitment, development or promotion purposes these programmes will provide objective assessment data to support interview observations.
Programmes include:
Our ongoing partnership with MGTS continues to play a vital role in the development of skilled engineering talent within our business. Their expertise, professionalism, and commitment to high-quality training are closely aligned with our own values and standards. Through this collaboration, we have established a strong and sustainable pipeline of capable apprentices who contribute positively to our operations.
We look forward to continuing this successful relationship.
The quality of teaching, learning and assessment is consistently good and supports apprentices to make good progress and succeed well.
In practical training areas, the quality and range of technical resources to support the training of engineering apprentices are impressive.

Get in touch
Our team are on hand to help with all your apprenticeship, training and upskilling requirements. We look forward to hearing from you.
024 7663 0333 enquiries@mgts.co.uk